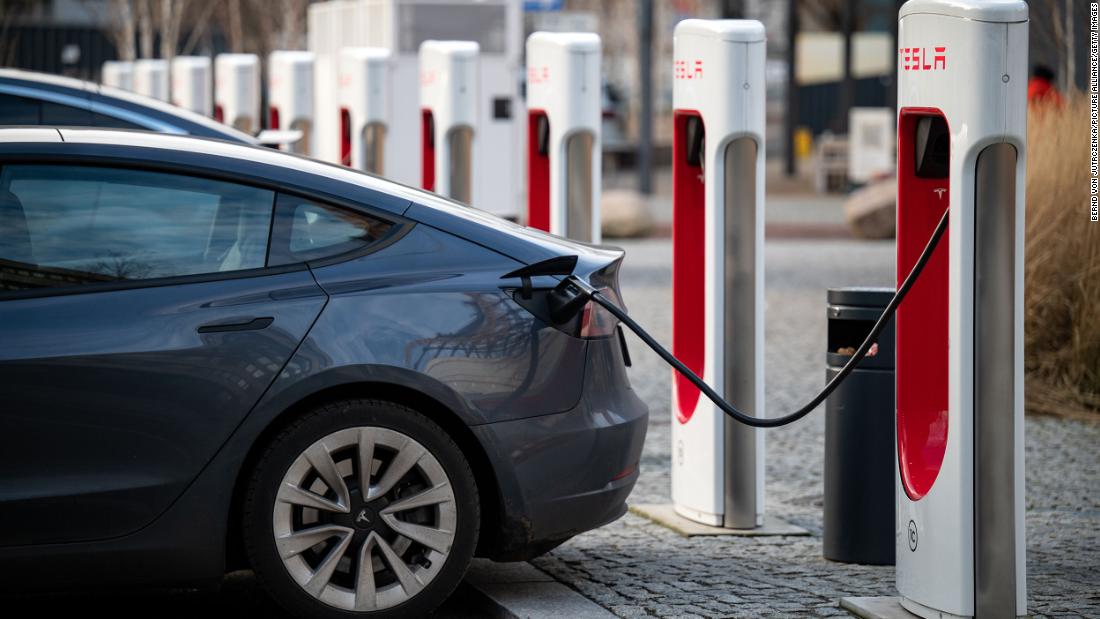
While his company lost, the battery Riley bet on — lithium iron phosphate, called LFP — is increasingly winning.
Demand for nickel and cobalt has surged in recent years and automakers are adopting strategies to hedge against the turbulent market. Tesla has changed its tune and said in April that nearly half of its vehicles sold in the first three months of the year do not include nickel or cobalt.
Batteries like what Riley envisioned are gaining popularity as automakers are increasingly interested in avoiding nickel and cobalt, which are rare as well as difficult and fraught to extract from the earth.
Riley is left watching other companies profit on the potential he saw.
“It’s really hard to see others capitalizing on what we saw all along,” Riley told CNN Business.
The growth of LFP batteries
Tesla and other automakers like China’s BYD have turned to the LFP battery, which was developed in America in the ’90s but later mostly cast aside in U.S. electric vehicles. Experts say the technology may give Tesla an edge over competitors who aren’t using it.
Battery metals are becoming as critically essential to the auto industry as oil has long been. A battery is simply a device that stores chemical energy for later conversion to electrical energy, and the chemistry used in different battery types greatly impacts their cost, safety, power and longevity.
The lithium iron phosphate batteries Tesla has invested in differ in the battery chemistry required to create the positive end of the battery during discharge, called the cathode. While the battery still requires lithium, it uses iron, which is abundant and cheap, instead of metals like cobalt and nickel.
LFP batteries emerged in 1997 from the lab of University of Texas professor John Goodenough, who later won the Nobel prize for chemistry for his research on lithium-ion batteries.
Although LFPs initially sparked excitement and investment in startups like Riley’s A123 Systems, interest cooled.
“The deficit was always energy density on a head-to-head comparison,” Riley said. “A123 didn’t win the business.”
In the US, car owners value a vehicle’s range, according to auto experts. The LFPs manufactured in the ’90s and aughts lagged far behind lithium-ion batteries in terms of the power they could hold, and therefore the number of miles a driver could travel on a single charge.
Because of this, the technology was largely avoided by American automakers. General Motors used LFP batteries in its electric Chevrolet Spark, which began US sales in 2013 and has since been discontinued. Today’s Chevrolet Bolt, the modern successor of the Spark, uses a battery with nickel and cobalt.
China now dominates the LFP market. Today, 44% of electric vehicles sold in China use LFP batteries, while 6% are in Europe, and 3% in the US and Canada, according to Benchmark Mineral Intelligence, which studies the battery industry.
Advances in LFP battery technology have expanded their range, according to battery experts. “We underestimated the ability of LFP to improve. It has come a long way,” Rodney Hooper, a partner at RK Equity who advises clients on lithium and batteries told CNN Business. Tesla now uses LFP batteries in most of its standard range vehicles. The standard-range Model 3 equipped with an LFP battery has 267 miles of range, which is comparable to the 280-mile range of the VW’s ID 4, which uses a lithium-ion battery that contains nickel and cobalt.
And beyond the benefits of avoiding cobalt and nickel extraction in their manufacture, the batteries have a number of advantages. LFP batteries are more stable and less likely to catch fire than batteries with nickel and cobalt, so fewer protections are needed.
LFPs also generally can be charged more times, which expands their lifecycle. They are able to charge to 100% on a regular basis, which isn’t recommended for cars with nickel and cobalt batteries as repeated full charges may diminish battery life. And LFPs have 20% fewer greenhouse gas emissions per unit of energy than typical nickel and cobalt batteries, according to Jarod Kelly, who studies sustainability at Argonne National Laboratory, a hotbed of battery research.
There are also tradeoffs: the batteries don’t perform as well in cold climates, and recycling LFPs isn’t as economically viable as recycling nickel and cobalt batteries.
Electric vehicle advocates often describe the promise of a “circular economy,” in which old electric vehicles batteries are recycled and turned into new batteries, making the world more sustainable. But if electric vehicles shift to LFPs, that may be less likely, according to battery experts. Recyclers have generally focused on nickel and cobalt, because their price and scarcity make them appealing to recycle.
“Recycling is important, but it also has to make sense in terms of the rationale,” Ajay Kochhar the CEO of battery recycler Li-Cycle told CNN Business. If it remains cheaper to mine new iron, there is little incentive to reclaim iron from used batteries. Governments or consumers may need to pay to have LFPs recycled.
Adopting LFPs may also make American businesses more dependent on Chinese suppliers, which dominate LFP production. Tesla executive Drew Baglino, asked about relying on China for LFPs on an earnings call in October, said the automaker’s goal is to localize key vehicle parts on the continent on which the vehicle is produced.
Still, automakers beyond Tesla have expressed their interest in LFP technology. Rivian told CNN Business in a statement that it sees “incredible potential” in LFPs. It first said last year that it planned to use LFPs for standard range vehicles. VW expects to use LFPs in its smaller cars. Ford has said it’s “looking at” LFPs.
Riley continues to try to push battery technology forward. He co-founded another startup, Conamix, which is trying to develop low-cost battery cathodes that are made of sulfur. Riley’s focus on batteries keeps him abreast of the success others are having with LFPs.
“It’s bittersweet, emotionally,” Riley said.