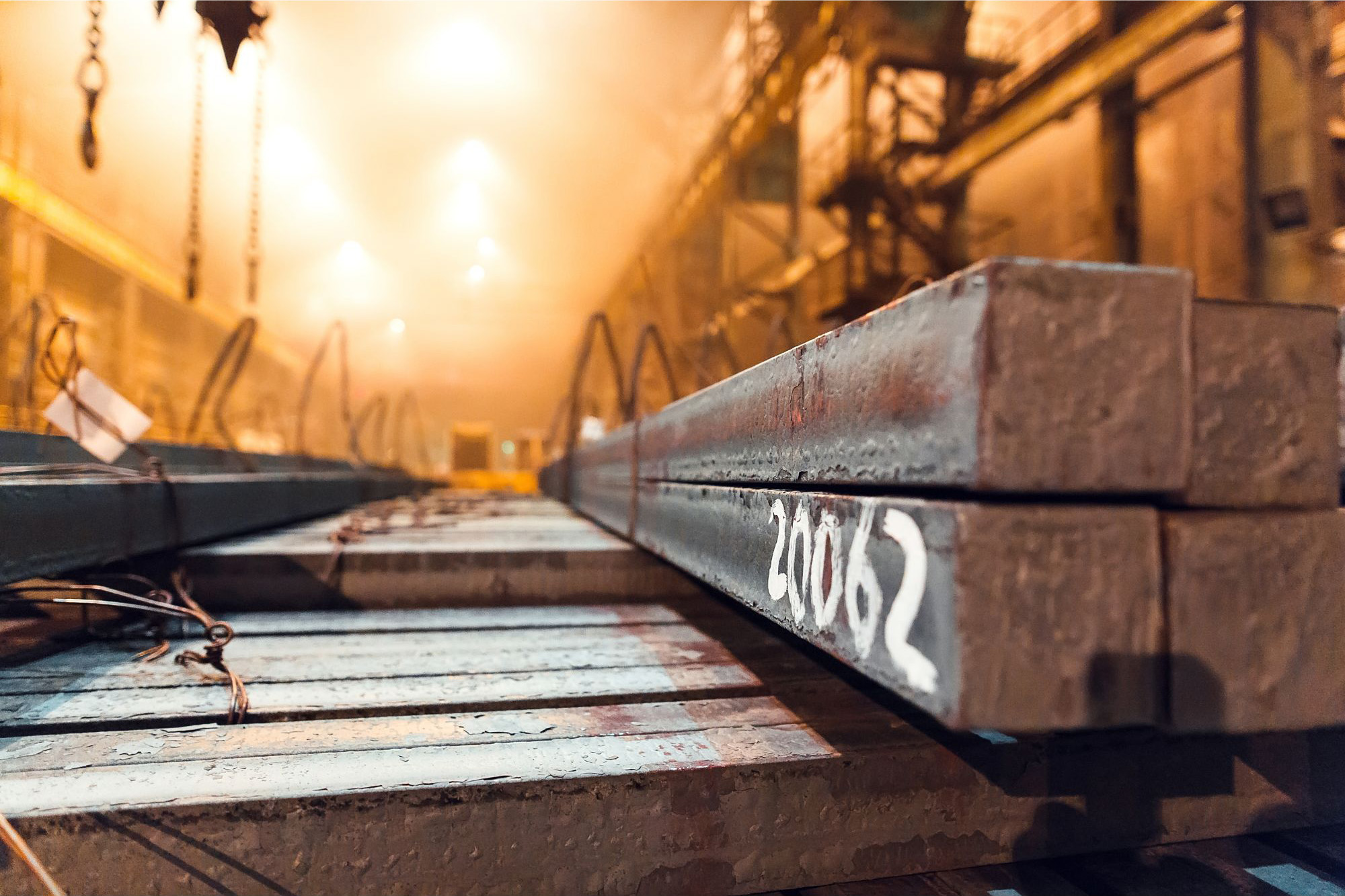
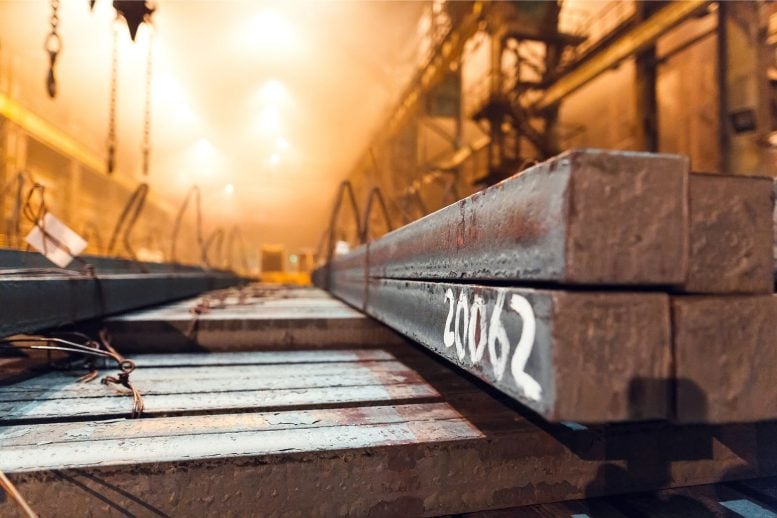
A UC Davis study reveals U.S. material production incurs $79 billion in yearly climate damages; pricing these costs could spur eco-friendly manufacturing.
A new study from engineers and economists at the University of California, Davis, reveals that producing materials like steel, plastics, and cement in the United States alone causes $79 billion annually in global climate-related damages. Factoring these costs into market prices could motivate a shift toward more climate-friendly alternatives.
“We wanted to look at the cost to society to produce these materials,” said Elisabeth Van Roijen, a recent Ph.D. graduate from the UC Davis Department of Civil and Environmental Engineering and lead author on the paper, published Oct. 24 in Environmental Research Letters.
Van Roijen, undergraduate researcher Paikea Colligan, and postdoctoral researcher Seth Kane set out to calculate the missing climate costs for producing nine common materials: aluminum, iron and steel, brick, cement, lime, gypsum, asphalt, glass, and plastics.
They gathered data on the amounts of these materials produced in the United States, the energy used to make them, and the greenhouse gas emissions from the manufacturing process. They assessed the climate costs of emissions using the Environmental Protection Agency’s Social Cost of Carbon standard. This is an estimate of the costs of carbon dioxide emissions, such as preventing, mitigating, and recovering from climate-related natural disasters.
The team calculated that 370 million tons of these nine materials were manufactured in the United States in 2018, resulting in 427 million tons of carbon dioxide emissions. This resulted in $79 billion of climate costs that are not included in the market prices of these materials.
Climate costs are affected by material demand. For example, manufacturing aluminum generates quite a lot of carbon dioxide per weight of the product, while making the same amount of brick generates much less. But the tonnage of bricks produced every year is far higher than that of aluminum, so making bricks contributes more to climate costs overall than making aluminum.
Steel and plastics have the highest overall contribution due to the very large demand for these materials.
Almost half of the costs from processes
Just under half of the climate costs – 42% – came from manufacturing processes, rather than energy use. For example, making cement produces carbon dioxide because of the chemical reactions involved, in addition to any energy consumed.
This is important because while climate costs of energy can be reduced by switching to renewable sources, process costs are fixed unless we can develop new processes or substitute materials.
“Alternative materials are a really important research area,” Van Roijen said. These could include supplements to partly replace cement in concrete and biomass-based plastics.
Incorporating climate costs shows that the real cost of manufacturing these materials is much higher than current market prices. Adopting policies that reflect these costs can create incentives to develop new, climate-friendly processes and materials.
“When considering new technologies, such as biomass-based plastics, if we can account for the benefit of carbon storage in the material, we can make them more cost-effective in the market,” Van Roijen said.
The manufacturing dataset will inform both practical and policy work, Kane said. The same methods could also be replicated for other sectors of the economy.
Reference: “The unaccounted-for climate costs of materials” by Paikea Colligan, Elisabeth Van Roijen, Seth Kane, Frances Moore and Sabbie A Miller, 24 October 2024, Environmental Research Letters.
DOI: 10.1088/1748-9326/ad796e
Additional authors on the paper are Sabbie Miller, associate professor in the UC Davis Department of Civil and Environmental Engineering and Frances Moore, associate professor in the Department of Environmental Science and Policy. The work was partly supported by the National Science Foundation and the U.S. Department of Energy’s Advanced Research Projects Agency – Energy.