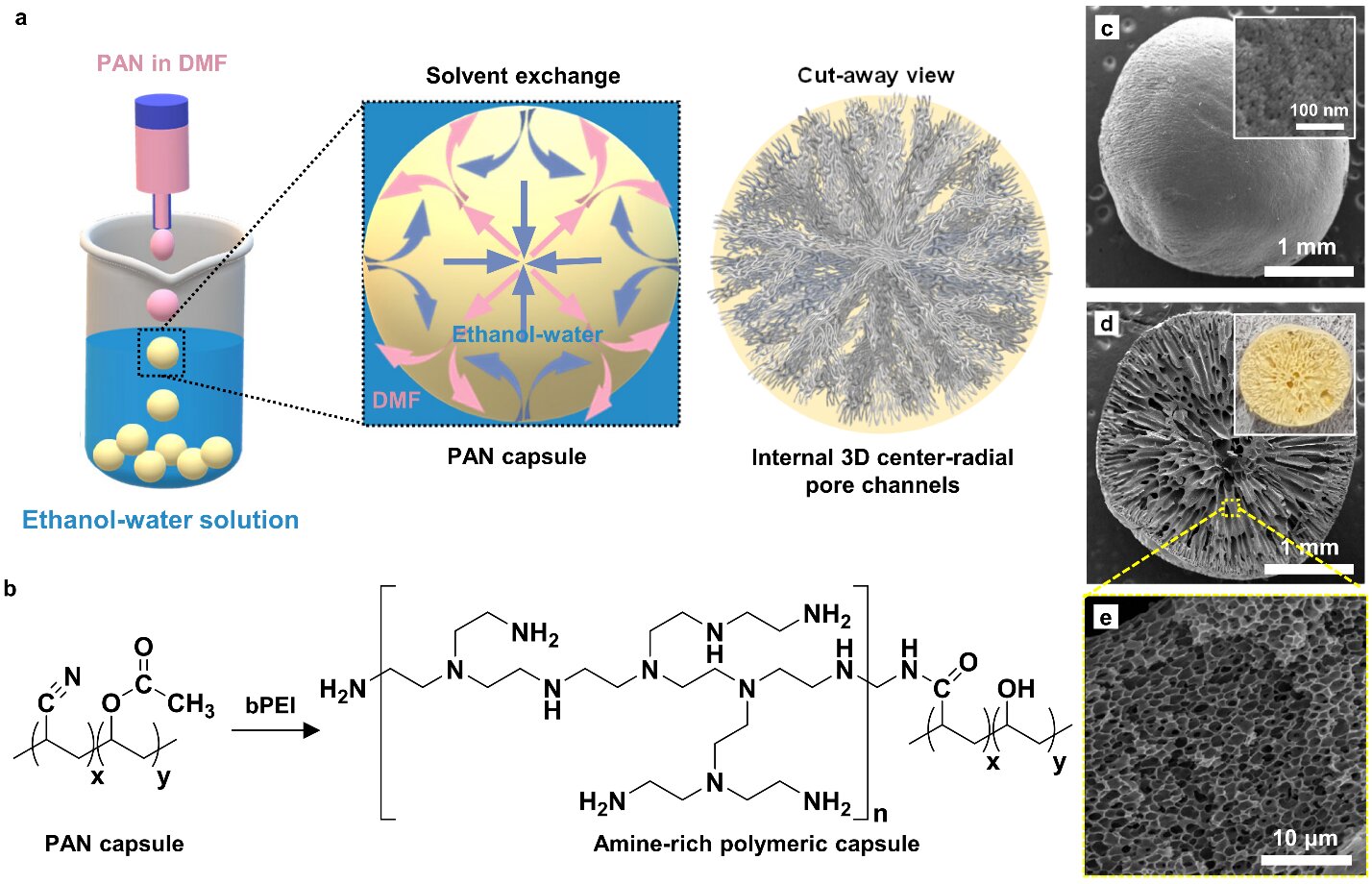
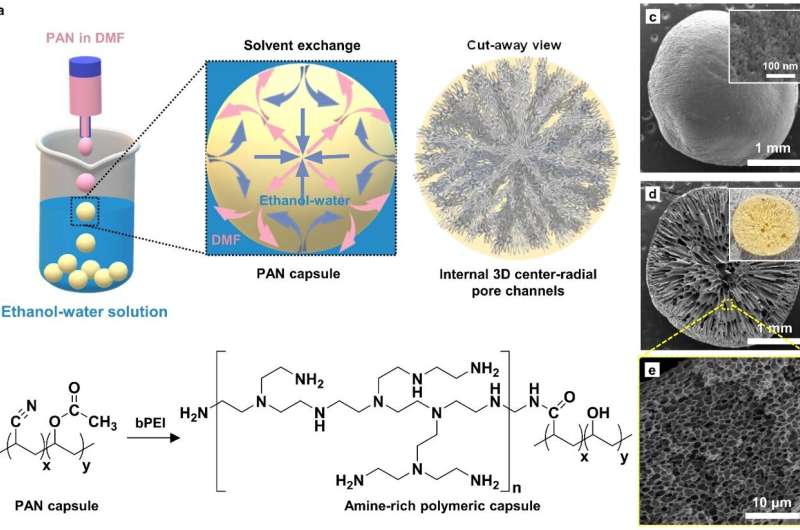
In South Korea, which relies on imports for 99.3% of its metal resources, the per capita consumption of those metal resources is the highest in the Organization for Economic Co-operation and Development, and consumption of precious metals in industries such as renewable energy, healthcare and semiconductors is increasing. Gold is in demand for applications such as batteries, electric vehicles and renewable energy in the electric and electronic industries, but is a big variable in the industry due to its limited availability and high cost. Thus, research on urban mining, which extracts precious metals from waste, is being actively conducted around the world. However, most of the technologies for extracting high-purity gold from waste resources require large amounts of chemicals and high operating temperatures; therefore, it has regulatory and efficiency problems.
A Korean research team has developed a technology that can dramatically increase the recovery rate of precious metals from waste. The research team, comprising Dr. Jae Woo Choi and Dr. Kyung-Won Jung from the Center for Water Cycle Research at the Korea Institute of Science and Technology (KIST), reported that they developed a gold recovery process with the world’s highest recovery efficiency of 99.9 %. The technology is a capsule-type material in which a polymeric shell surrounds a multi-layered internal structure.
The developed material has the advantage of high recovery efficiency compared to conventional adsorption materials since the material traps gold ions inside the capsule for recovery. The material also has the advantage of preventing the clogging of the internal porous structure since the polymeric shell allows gold ions to penetrate while being impermeable to suspended solids present with gold. By introducing functional groups that react only with gold ions in the multi-layered internal structure, gold that has passed through the polymeric shell could be stably recovered even with the coexistence of 14 types of ions and 3 types of suspended solids. Capsule-type material can be produced through a continuous process based on the solvent exchange method, and its efficiency and stability were demonstrated by maintaining a recovery performance of 99.9% or more even when the material was reused 10 times.
-
Gold recovery concept of material (left) and its performance (right). Credit: Korea Institute of Science and Technology (KIST)
-
(From left) gold-containing waste liquid, a capsule-type material wrapped in a circular polymeric shell (white) developed by KIST researchers to recover gold in an eco-friendly manner, gold extracted through the recovery process, and recovered gold refined into high-purity gold. Credit: KIST
The authors write, “The material developed through this research solves the problems of conventional materials developed for the recovery of precious metals. Moreover, it can be immediately applied to related industrial processes as they can be easily synthesized in large quantities. Through this study, it was evident that the chemical properties and morphology of the recovered material could also play a very important role in recovering metal resources from the water.”
The lead author, Dr. Youngkyun Jung of KIST, said, “The results of this research are expected to serve as a basis for the development of the first eco-friendly process in Korea that can selectively recover and refine metal resources from waste and precious metal scraps generated in various industries, such as automobiles and petrochemicals.”
The results of the research were published in the latest issue of the Chemical Engineering Journal.
Development of high-durability single-atomic catalyst using industrial humidifier
Youngkyun Jung et al, Cage-like amine-rich polymeric capsule with internal 3D center-radial channels for efficient and selective gold recovery, Chemical Engineering Journal (2022). DOI: 10.1016/j.cej.2022.135618
Provided by
National Research Council of Science & Technology
Citation:
New technology dramatically increases the recovery rate of precious metals from waste (2022, May 17)
retrieved 17 May 2022
from https://phys.org/news/2022-05-technology-recovery-precious-metals.html
This document is subject to copyright. Apart from any fair dealing for the purpose of private study or research, no
part may be reproduced without the written permission. The content is provided for information purposes only.