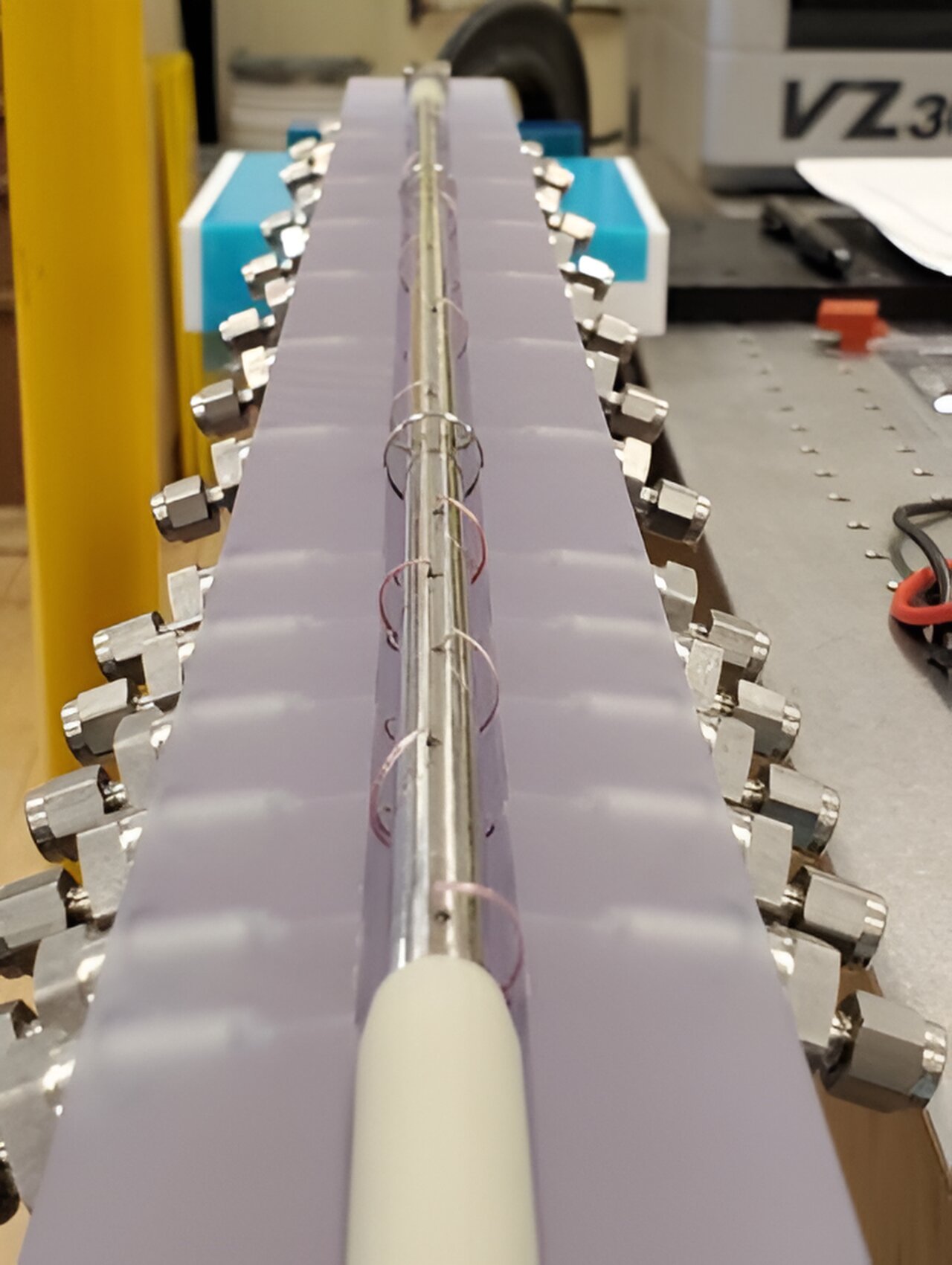
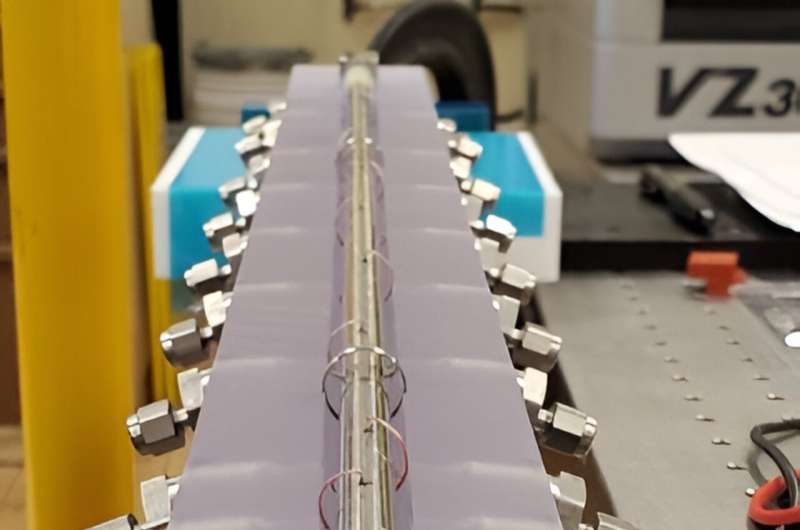
Planes, trains, automobiles… and spacecraft. While all four of these transportation innovations rely on fuel for power, another key component is thermal management. Without controlling the distribution and flow of heat inside a system, such as the International Space Station and other commercial spacecraft, temperatures inside the vessels would not be habitable for astronauts given the extreme hot and cold temperatures of outer space.
This complex issue is just one of the many challenges being investigated by NASA’s Physical Sciences researchers at Glenn Research Center through the Flow Boiling and Condensation Experiment (FBCE).
Two-phase flow innovation
Findings from FBCE’s Condensation Module for Heat Transfer (CM-HT) are expected to play a vital role in the design of future space and Earth systems. This includes space power generation, planetary habitat, space vehicle temperature control, cryogenic fluids storage, waste management, electric vehicle charging, fighter aircraft cooling under varying g-loads, and regenerative fuel cells.
The scientific objectives of CM-HT aim to generate a database in flow condensation which will be used for assessing the condensation heat transfer in microgravity as well as developing criteria for flow condensation gravity independence. Such criteria will be used for designing efficient flow condensers for space applications. Flow condensation mathematical predictive models, Computational Fluid Dynamics (CFD) models, and design correlations will be developed for design applications.
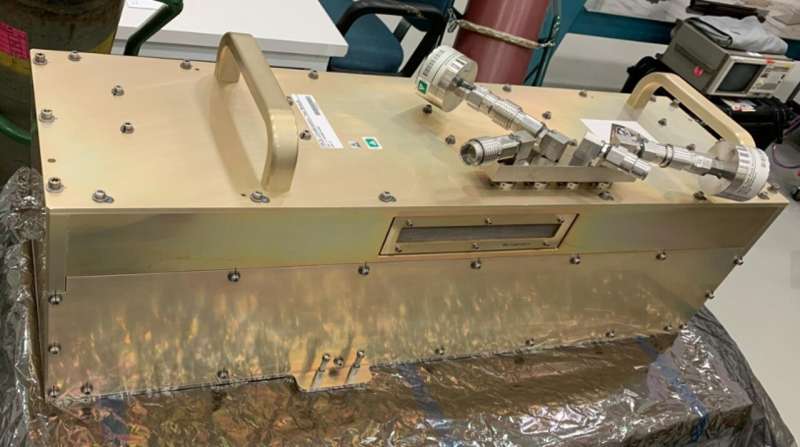
Achieving equilibrium in microgravity
The FBCE will serve as a primary platform for obtaining two-phase flow boiling and condensation heat transfer data in microgravity. The CM-HT test module will feature a thin-walled stainless-steel tube concentrically positioned along another cylindrical channel formed into a highly thermal insulative material.
The test fluid vapor will flow through the inner tube and condense by rejecting heat to a counterflow of water through the annulus. Low thermal conductivity of the outer channel wall will ensure that all the heat is transferred between the two fluids. Because of its low thermal conductivity compared to other metals, stainless steel minimizes axial conduction effects, allowing mostly radial heat transfer between the fluids.
By comparing the microgravity heat transfer data against data obtained in Earth’s gravity, it will be possible to ascertain the influence of body forces on two-phase transport phenomena in pursuit of mechanistic models as well as correlations, and to help determine the minimum flow criteria to ensure gravity independent flow boiling and condensation.
Low velocity two-phase flow in microgravity poses serious challenges not commonly encountered in Earth’s gravity. As the gravity level is reduced, a new balance comes into play between inertial, surface tension and body forces, so that the basic mechanics of the flow interfacial structure drastically change. To study these effects, the FBCE facility was installed on the ISS Fluid Integrated Rack (FIR) orbiting laboratory that offers a great microgravity environment for two phase flow research.
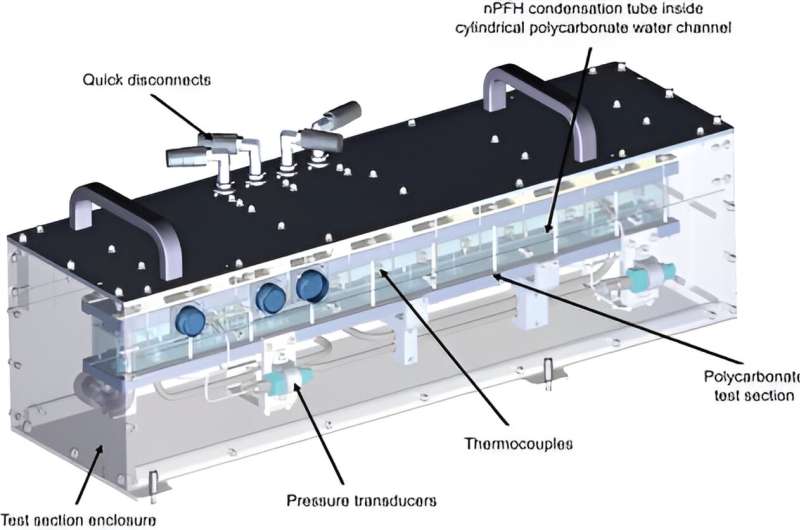
Improved power efficiency and energy conservation
Flow boiling and condensation have been identified as two key mechanisms for heat transport that are vital for achieving weight and volume reduction, as well as performance enhancement in future space systems. Results from this investigation will ultimately support optimization of the design of flow boilers and flow condensers for utilization in long duration missions with high power demand in the microgravity environment. Efficient boilers and condensers result in efficient use of energy on long duration missions. Since space systems operate on a limited power budget, placing stringent constraints on the power available will additionally benefit missions’ energy conservation.
These space-based studies will also advance heat transfer mechanisms on Earth by optimizing heat exchanger performance. Improved electric vehicle charging times, rocket engine cooling, and fighter jet propulsion systems are all just a few of the mechanical systems on Earth that will also benefit from this space technology.
Citation:
Optimizing heat exchange flow in microgravity (2023, July 31)
retrieved 1 August 2023
from https://phys.org/news/2023-07-optimizing-exchange-microgravity.html
This document is subject to copyright. Apart from any fair dealing for the purpose of private study or research, no
part may be reproduced without the written permission. The content is provided for information purposes only.