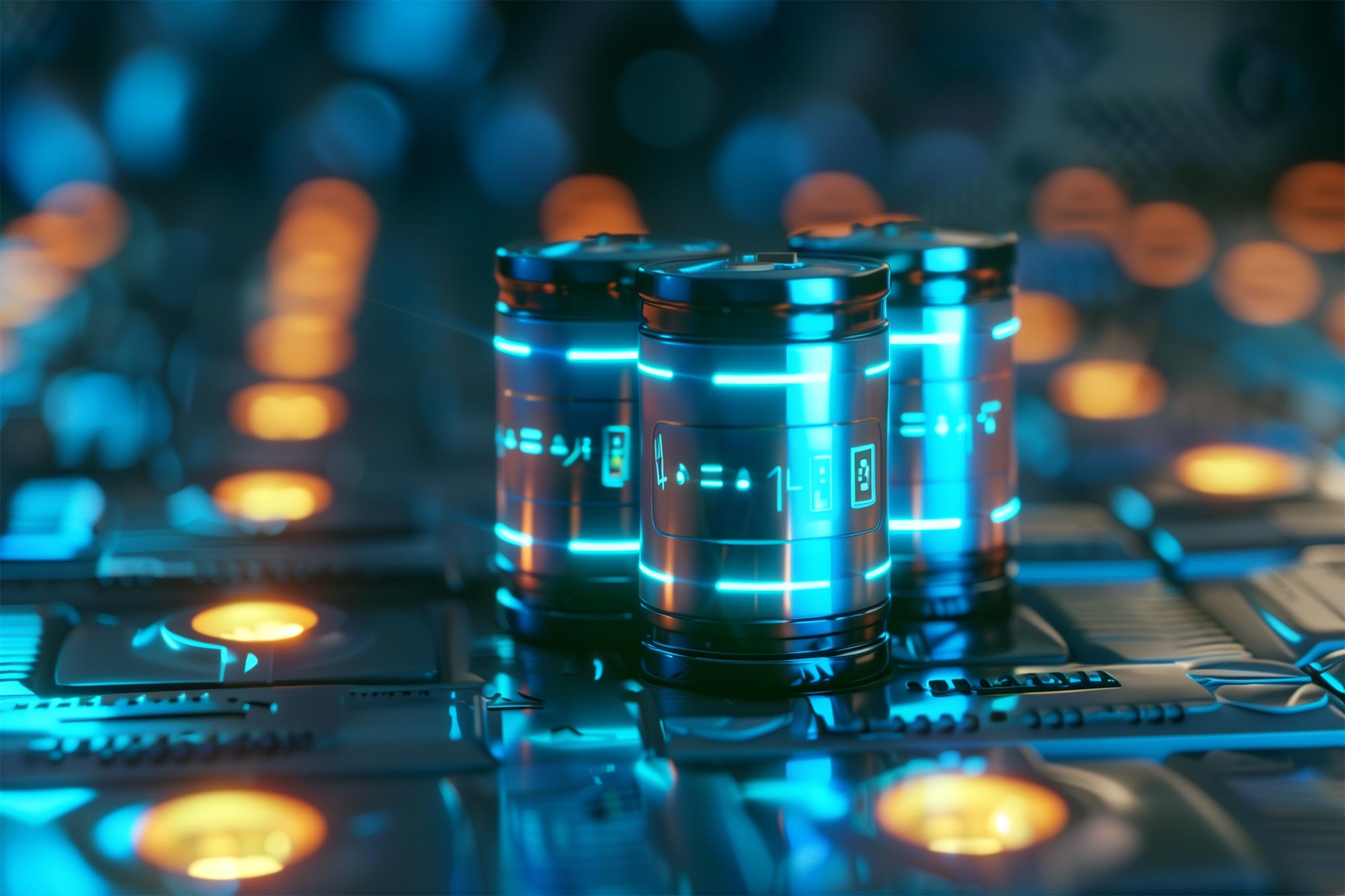
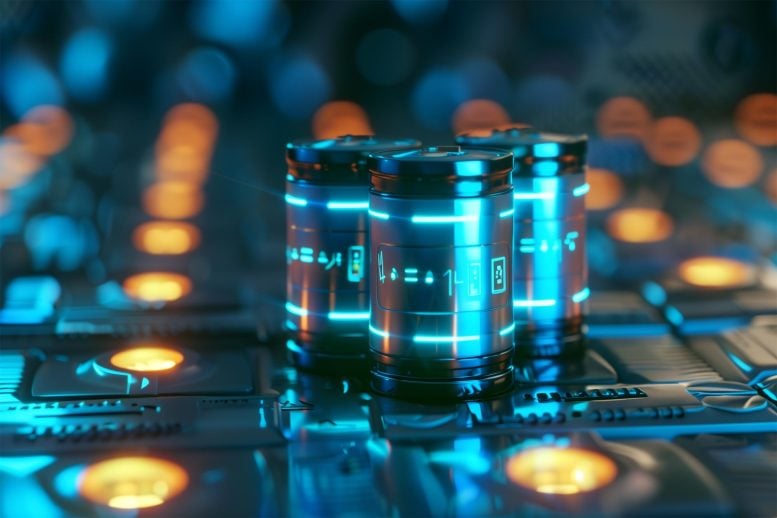
Researchers at Cornell have engineered a groundbreaking porous crystal using a unique fusion of macrocycle and molecular cage structures, enhancing lithium-ion transport in solid-state batteries.
This new crystal design features one-dimensional nanochannels that significantly increase ion conductivity, a development that promises safer batteries and has potential applications in water purification and bioelectronics.
By fusing two contorted molecular structures, Cornell researchers have developed a porous crystal capable of absorbing lithium-ion electrolytes and smoothly transporting them through one-dimensional nanochannels. This innovative design has the potential to enhance the safety of solid-state lithium-ion batteries.
The team’s findings are detailed in the paper “Supramolecular Assembly of Fused Macrocycle-Cage Molecules for Fast Lithium-Ion Transport,” recently published in the Journal of the American Chemical Society. The lead author is Yuzhe Wang ’24.
The project was led by Yu Zhong, assistant professor of materials science and engineering in Cornell Engineering and the paper’s senior author, whose lab specializes in synthesizing “soft” and nanoscale materials that can advance energy storage and sustainability technologies.
Zhong had just joined Cornell’s faculty two years ago when he was contacted by Wang, an undergraduate transfer student beginning his junior year, who was enthusiastic about taking on a research project.
Designing Safer Lithium-Ion Batteries
At the top of Zhong’s list of potential topics was finding a way to make a safer lithium-ion battery. In conventional lithium-ion batteries, the ions are shuttled along via liquid electrolytes. But liquid electrolytes can form spiky dendrites between the battery’s anode and cathode, which short out the battery or, in rare cases, explode.
Solid-state batteries are generally safer but also present unique challenges. In these batteries, ions travel more slowly through solid materials due to increased resistance. To overcome this, Zhong aimed to create a new type of porous crystal that could facilitate ion movement along a designated pathway. This pathway needed to allow for smooth travel with minimal interaction between the lithium ions and the crystal structure, preventing the ions from sticking. Additionally, the crystal needed to accommodate a high concentration of ions to maintain efficient conductivity.
Innovative Molecular Fusion
Supported by a grant from the college’s Engineering Learning Initiatives, Wang went to work and devised a method of fusing together two eccentric molecular structures that have complementary shapes: macrocycles and molecular cages.
Macrocycles are molecules with rings of 12 or more atoms, and molecular cages are multi-ringed compounds that more or less resemble their name.
“Both macrocycles and molecular cages have intrinsic pores where ions can sit and pass through,” Wang said. “By using them as the building blocks for porous crystals, the crystal would have large spaces to store ions and interconnected channels for ions to transport.”
Achieving Record High Ionic Conductivity
Wang fused the components together, with a molecular cage at the center and three macrocycles radially attached, like wings or arms. These macrocycle-cage molecules use hydrogen bonds and their interlocking shapes to self-assemble into larger, more complicated, three-dimensional crystals that are nanoporous, with one-dimensional channels – “the ideal pathway for the ion to transport,” according to Zhong – that achieve ionic conductivity of up to 8.3 × 10-4 siemens per centimeter.
“That conductivity is the record high for these molecule-based, solid-state lithium-ion-conducting electrolytes,” Zhong said.
Detailed Structural Analysis and Applications
Once the researchers had their crystal, they needed to better understand its makeup, so they collaborated with Judy Cha, Ph.D. ’09, professor of materials science and engineering, who used scanning transmission electron microscopy to explore its structure, and Jingjie Yeo, assistant professor of mechanical and aerospace engineering, whose simulations clarified the interactions between the molecules and lithium ions.
“So with all the pieces together, we eventually established a good understanding of why this structure is really good for ion transport, and why we get such a high conductivity with this material,” Zhong said.
In addition to making safer lithium-ion batteries, the material could also be potentially used to separate ions and molecules in water purification and to make mixed ion-electron-conducting structures for bioelectronic circuits and sensors.
Exploring Future Applications
“This macrocycle-cage molecule is definitely something new in this community,” Zhong said. “The molecular cage and macrocycle have been known for a while, but how you can really leverage the unique geometry of these two molecules to guide the self-assembly of new, more complicated structures is kind of an unexplored area. Now in our group, we are working on the synthesis of different molecules, how we can assemble them and make a molecule with a different geometry, so we can expand all the possibilities to make new nanoporous materials. Maybe it’s for lithium-ion conductivity or maybe for even many other different applications.”
Reference: “Supramolecular Assembly of Fused Macrocycle-Cage Molecules for Fast Lithium-Ion Transport” by Yuzhe Wang, Kaiyang Wang, Qing Ai, Stephen D. Funni, Ashutosh Garudapalli, Qiyi Fang, Suin Choi, Gangbin Yan, Shayan Louie, Chong Liu, Jun Lou, Judy J. Cha, Jingjie Yeo, Zexin Jin and Yu Zhong, 9 September 2024, Journal of the American Chemical Society.
DOI: 10.1021/jacs.4c08558
Co-authors include doctoral student Kaiyang Wang, M.S. ’19; master’s student Ashutosh Garudapalli; postdoctoral researchers Stephen Funni and Qiyi Fang; and researchers from Rice University, University of Chicago and Columbia University.
The research was supported by Cornell Engineering’s Engineering Learning Initiatives.
The researchers made use of the Cornell Center for Materials Research and the Columbia University Materials Research Science and Engineering Center, both of which are funded by the National Science Foundation’s Materials Research Science and Engineering Center program.